Processo de Vulcanização na Indústria da Borracha
História, Técnicas, Impactos e Inovações
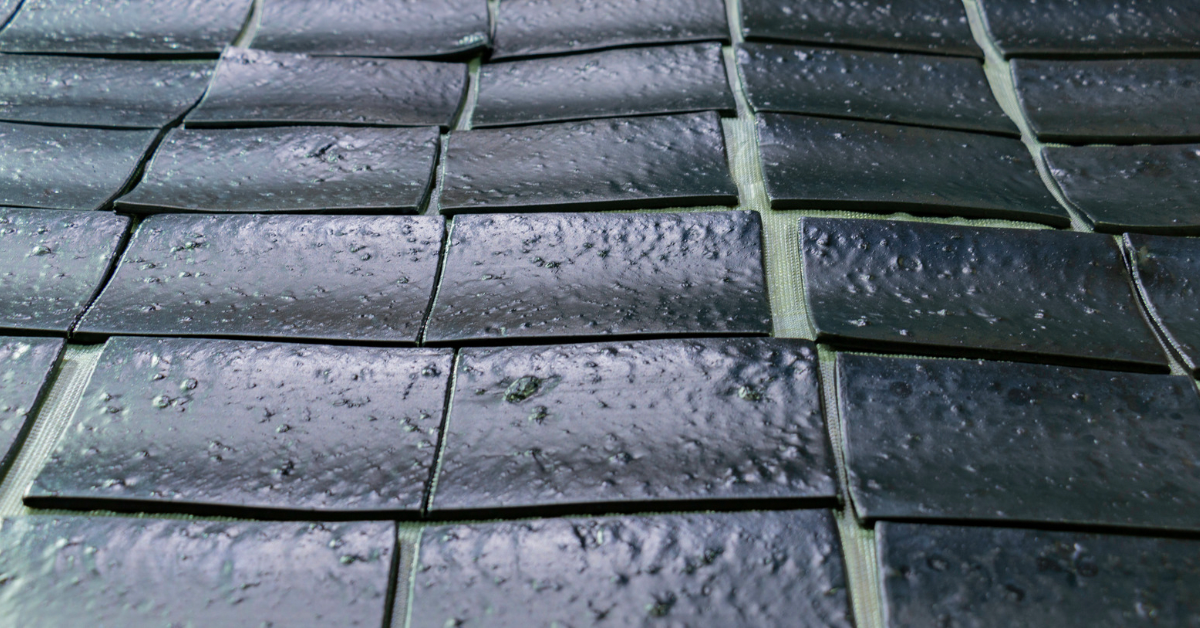
Você sabia que, antes da vulcanização, a borracha era praticamente inutilizável em muitas aplicações? Sem este processo, objetos de borracha amoleciam e ficavam pegajosos no calor e, no frio, endureciam a ponto de rachar.
A descoberta acidental da vulcanização pelo norte-americano Charles Goodyear, em 1839, revolucionou a indústria da borracha. Desde então, a vulcanização tornou-se a etapa fundamental para transformar borracha crua em materiais duráveis e elásticos, viabilizando produtos que vão de pneus a peças médicas.
Neste artigo, exploramos a história e evolução desse processo, comparamos técnicas clássicas e modernas, analisamos seu impacto industrial, discutimos desafios ambientais e destacamos as tendências e inovações que estão moldando o futuro da vulcanização.
História e Evolução da Vulcanização
A história da vulcanização começa no século XIX, quando a borracha natural era vista como um material promissor, porém problemático. Na época, apesar de ser usada em itens como capas impermeáveis e bolas, a borracha não tratada apresentava sérios inconvenientes: tornava-se mole e grudenta em dias quentes e rígida e quebradiça em dias frios.
Essa instabilidade limitava muito suas aplicações industriais. Foi nesse contexto que Charles Goodyear dedicou anos de experimentos para “domar” a borracha. Em 1839, Goodyear acidentalmente deixou cair uma mistura de borracha com enxofre sobre uma superfície quente. Para sua surpresa, o material resultante não derreteu completamente nem permaneceu pegajoso; em vez disso, formou-se um pedaço elástico com consistência semelhante ao couro. Ele percebera que a adição de enxofre, combinada ao calor, havia modificado a estrutura da borracha, tornando-a resistente a variações de temperatura.
Após refinar o método, Goodyear patenteou o processo em 15 de junho de 1844, batizando-o de vulcanização – uma referência a Vulcano, deus romano do fogo. Quase simultaneamente, na Inglaterra, Thomas Hancock desenvolveu um processo similar e também obteve patentes, consolidando a vulcanização como uma descoberta global.
A importância dessa invenção não pode ser exagerada. Borracha vulcanizada rapidamente se tornou a base para uma série de produtos que impulsionaram a Revolução Industrial tardia. A indústria automotiva, por exemplo, foi diretamente beneficiada: somente com borracha vulcanizada foi possível produzir pneus duráveis, melhorando drasticamente a segurança e o desempenho dos veículos.
No final do século XIX, a borracha já era uma commodity estratégica, e a vulcanização pavimentou o caminho para a expansão global desse mercado. Novas plantações de seringueiras surgiram para suprir a demanda crescente por borracha natural, ao mesmo tempo em que inventores buscavam criar borrachas sintéticas para complementar a oferta.
Ao longo do tempo, o processo de vulcanização continuou evoluindo. Nas formulações originais de Goodyear e Hancock, utilizavam-se grandes quantidades de enxofre e longos tempos de aquecimento para obter melhorias nas propriedades do material. Contudo, esses vulcanizados iniciais ainda não eram ideais. Somente décadas depois veio um dos maiores avanços: a descoberta dos aceleradores orgânicos de vulcanização no início do século XX.
Por volta de 1906, químicos como Karl Oenslager perceberam que certas substâncias (como anilina, posteriormente substituída por compostos menos tóxicos) aceleravam enormemente a cura da borracha. Os aceleradores permitiram vulcanizar em menor tempo e temperatura, usar menos enxofre e ainda assim obter borracha com propriedades mecânicas superiores. Com eles, reduziu-se a degradação térmica e o envelhecimento precoce do material, além de viabilizar a incorporação de cargas reforçantes (como o negro-de-fumo) sem prejudicar a reação de cura. Esse progresso químico abriu caminho para a era dos pneus modernos e inúmeros artefatos de borracha com desempenho muito aprimorado ao longo do século XX.
Técnicas Clássicas e Modernas de Vulcanização
Método Tradicional com Enxofre
No método clássico desenvolvido por Goodyear, a vulcanização consiste em misturar borracha crua com enxofre e, em seguida, aplicar calor e pressão controlados para promover uma reação química entre eles.
O enxofre cria ligações cruzadas entre as longas moléculas poliméricas da borracha, resultando em uma rede tridimensional. Quando a quantidade de ligações cruzadas é adequada, a borracha deixa de fluir como um termoplástico e adquire uma forma fixa, porém permanece flexível e elástica – essa é a característica chave de um material vulcanizado. Em outras palavras, a vulcanização “trava” as moléculas, impedindo que o material derreta no calor ou fique frágil no frio.
Nos primórdios, esse processo tradicional com enxofre era lento e exigia temperaturas elevadas. Vulcanizar uma peça podia levar horas, e frequentemente era necessário teor alto de enxofre, o que deixava resíduos e até tornava o produto final amarelado ou com florescimento de enxofre na superfície. Com o tempo, introduziu-se ao mix ingredientes auxiliares para tornar a vulcanização mais eficiente. Um marco tecnológico foi a inclusão de aceleradores na mistura. A adição de pequenas quantidades de aceleradores orgânicos (como derivados de aminas, tiuram e benzotiazóis) catalisa a reação entre a borracha e o enxofre. Isso permitiu vulcanizar em temperaturas mais baixas e reduzir drasticamente o tempo de cura, evitando inclusive a decomposição oxidativa da borracha durante o processo.
Além disso, com os aceleradores foi possível diminuir a quantidade de enxofre necessária na formulação, melhorando a resistência ao envelhecimento e às intempéries do produto vulcanizado. Em suma, o sistema “enxofre + acelerador + ativadores” (como óxido de zinco e ácido esteárico) tornou-se o padrão das vulcanizações convencionais, garantindo eficiência e qualidade. Até hoje, a maioria das borrachas naturais e de muitos elastômeros sintéticos insaturados (por exemplo, SBR e NBR) são curados pelo método de enxofre com aceleradores, graças ao seu balanço entre custo e desempenho.
Agentes de Cura Modernos: Peróxidos e Vulcanização sem Enxofre
Com o desenvolvimento de novos polímeros no século XX, nem sempre o sistema de enxofre tradicional era adequado. Surgiram técnicas modernas de vulcanização que empregam outros agentes de cura, muitas vezes sem enxofre. De modo geral, a maioria dos agentes vulcanizantes não sulfurados se enquadra em três categorias: peróxidos orgânicos, óxidos metálicos e compostos difuncionais (como certas resinas).
Essas alternativas expandiram as possibilidades de cura, atendendo às necessidades de elastômeros especiais e aplicações de alto desempenho.
Um dos métodos modernos mais difundidos é a vulcanização por peróxidos. Em vez de enxofre, utilizam-se peróxidos orgânicos (como peróxido de dicumila, por exemplo) que geram radicais livres quando aquecidos. Esses radicais provocam a formação de ligações carbono-carbono diretas entre as cadeias do polímero.
Diferentemente da vulcanização sulfidílica, em que pontes de enxofre conectam as moléculas, aqui obtém-se uma rede de ligações covalentes C–C. Essa técnica é especialmente útil para borrachas que possuem pouca ou nenhuma insaturação em sua cadeia, nas quais o enxofre tradicional teria dificuldade de reagir. Elastômeros saturados como o EPDM (sem terceiros monômeros dieno) e a borracha de silicone são tipicamente curados por peróxidos, já que não contêm duplas ligações suficientes para o método com enxofre. A vantagem do sistema peróxido é obter vulcanizados com excelente resistência térmica e menor deformação remanescente, pois as ligações C–C são mais estáveis a altas temperaturas. Além disso, não há formação de subprodutos como gás sulfídrico e geralmente o produto final tem menos odor. Por outro lado, a vulcanização por peróxido exige formulações bem controladas – certos aditivos como óleos plastificantes ou antioxidantes podem reagir com os radicais e inibir a cura, demandando ajustes na composição. Ainda assim, esse método tornou-se indispensável em artefatos que requerem alta pureza (por exemplo, artigos médicos de silicone) ou estabilidade térmica superior (cabos elétricos, vedações de motor, etc.).
Outro exemplo de cura sem enxofre são os sistemas à base de óxidos metálicos. Certas borrachas reagem em presença de óxido de zinco ou magnésio para formar ligações cruzadas iônicas. Um caso clássico é o policloropreno (Neoprene), que vulcaniza eficientemente com uma combinação de ZnO e MgO, dispensando enxofre em sua formulação. Também há borrachas nitrílicas carboxiladas que se reticulam através de pontes formadas entre grupos carboxila e óxidos metálicos.
Esses sistemas geram vulcanizados com boas propriedades adesivas e de resistência, sem o inconveniente de liberação de enxofre livre – o que é benéfico, por exemplo, para borrachas claras ou coloridas que manchariam com enxofre.
Além dos óxidos, diversos agentes bifuncionais inovadores foram introduzidos como alternativas de vulcanização. Resinas fenólicas (resinas de alquilfenol-formaldeído, também chamadas de “resinas de quinona”) são empregadas para vulcanizar borracha butílica e halobutílica, criando ligações cruzadas tipo carbono-carbono e carbono-oxigênio. Compostos como o p-quinona dioxima em combinação com óxido de zinco são utilizados para vulcanizar borracha butílica, oferecendo resistência especial à tensão e ao envelhecimento.
Já as borrachas fluoradas (FKM, como o Viton) não respondem nem a enxofre nem a peróxidos convencionais, de modo que utilizam diaminas especiais ou agentes à base de di-hidroxi (bisfenóis) para alcançar a reticulação necessária. Cada um desses sistemas “exóticos” foi desenvolvido para atender demandas particulares de novos elastômeros sintéticos ao longo do último século.
Em suma, as técnicas modernas de vulcanização diversificaram os caminhos para curar borracha, indo muito além do enxofre elementar. Hoje, engenheiros de polímeros podem escolher entre uma variedade de agentes vulcanizantes – ou até combinar mais de um – para obter as propriedades desejadas em cada aplicação. Inclusive, há processos que utilizam energia de radiação (micro-ondas ou feixes de elétrons) para vulcanizar certos artefatos contínuos, sem adição de qualquer agente químico. Por exemplo, perfis extrudados de borracha podem passar por um túnel de micro-ondas que os aquece rapidamente e realiza a vulcanização de forma contínua e sem pressão, com complemento de calor via ar quente, aumentando a produtividade.
Essas inovações refletem a constante busca da indústria por eficiência e controle no processo de cura, seja adaptando novas fontes de energia, seja desenvolvendo novos reagentes.
Impacto na Indústria da Borracha
A vulcanização teve um impacto transformador na indústria da borracha, possibilitando o surgimento de um vasto leque de produtos essenciais no mundo moderno. Após sua descoberta, artigos de borracha antes impraticáveis tornaram-se viáveis, impulsionando diversos setores industriais. Alguns exemplos notáveis de aplicações de borracha vulcanizada incluem:
- Pneus e Produtos Automotivos: Os pneus são, sem dúvida, o carro-chefe do uso de borracha vulcanizada. A capacidade de suportar deformações contínuas, atrito elevado e diferentes climas só é possível graças à rede de ligações cruzadas formada na vulcanização, que garante resistência e elasticidade. Além dos pneus, inúmeras peças automotivas utilizam borracha vulcanizada, como vedações de óleo e água, mangueiras do sistema de arrefecimento, buchas de suspensão e componentes antivibração (coxins de motor). A introdução dos pneus vulcanizados no final do século XIX e começo do XX melhorou drasticamente a confiabilidade dos veículos, tornando viagens mais seguras e confortáveis. Até hoje, cerca de 70% de toda borracha produzida globalmente é destinada à fabricação de pneus e produtos relacionados ao transporte.
- Selos, Vedações e Peças Industriais: A capacidade da borracha vulcanizada de manter sua forma sob compressão e vedar líquidos ou gases a torna perfeita para guarnições e selos industriais. Juntas de vedação em motores e máquinas, o-rings em conexões hidráulicas, membranas e diafragmas em equipamentos – todos se beneficiam da estanqueidade proporcionada por um elastômero vulcanizado de qualidade. Correias transportadoras utilizadas em minas e fábricas também são feitas de borracha reforçada e vulcanizada, unindo elasticidade com resistência mecânica para movimentar toneladas de material sem rupturas.
- Artefatos de Consumo e Médicos: Calçados com solados de borracha vulcanizada, iniciados com as famosas galochas e tênis vulcanizados, aumentaram a durabilidade e conforto dos sapatos. Artigos esportivos, como bolas e pneus de bicicleta, passaram a resistir ao uso intenso. Na área médica, a vulcanização permitiu a fabricação de luvas cirúrgicas flexíveis e esterilizáveis (usando látex vulcanizado) e de tubos de borracha que não se dissolvem com calor. Até mesmo fios elásticos de roupas íntimas e equipamentos de proteção dependem da estabilidade conferida pela vulcanização. A borracha vulcanizada está presente em mangueiras, luvas, correias, peças de máquinas, calçados e muitos outros objetos do dia a dia, demonstrando o quão onipresente ela se tornou após a adoção desse processo.
Além das aplicações, o processo de vulcanização também influenciou o desenvolvimento de borrachas sintéticas ao longo do século XX. Durante a Segunda Guerra Mundial, quando o acesso à borracha natural ficou escasso, vários tipos de borracha sintética (como o SBR – estireno-butadieno e o BR – borracha de butadieno) foram produzidos em larga escala. Esses polímeros sintéticos tiveram que ser formulados para vulcanizar de forma eficaz, e a experiência prévia com aceleradores e aditivos foi crucial para adaptá-los. Em geral, borrachas naturais e sintéticas compartilham o princípio básico da vulcanização – ambas precisam de ligações cruzadas para atingir propriedades úteis – porém há diferenças importantes no processo de cura de cada uma. A borracha natural (poliisopreno natural) possui alto teor de ligações duplas em sua cadeia, o que a torna muito reativa com enxofre. Por isso, vulcaniza rapidamente e produz artefatos com excelente resiliência e resistência à rasgo. Já as borrachas sintéticas variam amplamente: algumas, como a SBR e a borracha nitrílica (NBR), também contêm duplas ligações (em seus monômeros de butadieno) e podem ser vulcanizadas com enxofre e aceleradores de maneira análoga à borracha natural.
Entretanto, outros elastômeros sintéticos foram projetados com estruturas diferentes para oferecer propriedades especiais, e isso afeta a forma como são vulcanizados.
Por exemplo, a borracha butílica (IIR), famosa por ser quase impermeável a gases, possui uns poucos átomos de insaturação, suficientes apenas para vulcanizar se usados agentes especiais (como resinas de quinona ou enxofre monoinsaturado) e altas doses de aceleradores. A EPDM, um terpolímero de etileno-propileno-dieno, é intencionalmente formulada com uma pequena quantidade de dieno para introduzir insaturações que permitam a vulcanização com enxofre; alternativamente, pode ser curada via peróxidos quando se busca ainda maior resistência ao envelhecimento. Já polímeros totalmente saturados, como certas borrachas de silicone e o EVA (acetato de vinila e etileno), não vulcanizam com enxofre de jeito nenhum – é necessário recorrer a peróxidos, radiação ou outros sistemas de reticulação.
Portanto, uma diferença-chave entre borracha natural e sintética está nos agentes de cura e condições necessárias. A natural geralmente vulcaniza fácil com enxofre e produz artigos de altíssima elasticidade, enquanto as sintéticas podem demandar receitas de cura sob medida. Em todos os casos, contudo, a vulcanização permanece como o coração do processamento da borracha, e avanços tecnológicos contínuos têm otimizado esse passo crucial.
Avanços Tecnológicos na Otimização da Vulcanização
Desde os tempos de Goodyear, tecnologias de otimização vêm aprimorando o processo de vulcanização para torná-lo mais rápido, controlável e econômico. Mencionar os aceleradores novamente é pertinente aqui: sua introdução no início do século XX não apenas acelerou a produção, mas também melhorou a qualidade dos vulcanizados (menos enxofre residual, melhor resistência ao envelhecimento, possibilidade de artigos translúcidos etc.).
Com o progresso da química, surgiram diversas classes de aceleradores (guanidinas, ditiocarbamatos, sulfenamidas, entre outros) que permitem aos formuladores ajustar o perfil de vulcanização: alguns proporcionam cura ultra-rápida para peças de ciclo curto, outros conferem um período de pré-vulcanização mais longo (maior scorch time) para permitir o fluxo do composto em moldes complexos antes de endurecer. Combinados a ativadores (como óxido de zinco) e retardadores (que evitam a vulcanização precoce durante a mistura), esses aditivos garantem um controle fino sobre quando e como a borracha irá vulcanizar.
No âmbito industrial, o design de equipamentos também evoluiu. Os antigos moldes em prensas hidráulicas aquecidas deram lugar a prensas modernas com controle preciso de temperatura e pressão, garantindo que cada centímetro do artefato cure uniformemente. A moldagem por injeção de borracha, por exemplo, permite que compostos sejam injetados em moldes fechados e vulcanizados rapidamente sob alta pressão – uma integração do processo de conformação e cura que aumentou muito a produtividade de peças técnicas (como vedações O-ring e conectores). Para produtos extrudados(perfis, mangueiras, cabos revestidos de borracha), adotaram-se linhas de vulcanização contínua: em vez de cortar comprimentos e vulcanizar em autoclave por batelada, a borracha sai da extrusora diretamente através de túneis de aquecimento (ar quente, sal derretido ou micro-ondas) onde é vulcanizada em movimento contínuo. Essas linhas contínuas eliminam emendas e aumentam a velocidade de produção consideravelmente.
No caso da vulcanização por micro-ondas, mencionada antes, o uso de energia eletromagnética de alta frequência aquece de dentro para fora compostos com polaridade (como borrachas de cloro ou nitrílicas), resultando em cura rápida do núcleo à superfície, algo difícil de conseguir apenas com calor convectivo.
Outra frente de avanço é a modelagem computacional e instrumentação. Atualmente, sensores e softwares permitem monitorar o grau de cura em tempo real, seja via medição de torque (reômetros e viscômetros de cure) ou até por técnicas dielétricas. Isso evita defeitos como subvulcanização (borracha “crua” no interior da peça) ou super-vulcanização(ressecamento e perda de propriedades por calor excessivo). Com tais ferramentas, os processos podem ser ajustados com precisão, garantindo qualidade consistente. Ademais, estudos de engenharia de materiais têm produzido formulações mais otimizadas, como os sistemas de vulcanização “EV” (efficient vulcanization), muito usados em pneus modernos, nos quais se utiliza um teor relativamente baixo de enxofre em combinação com aceleradores do tipo sulfenamida. Esses sistemas EV formam ligações cruzadas mono-sulfídicas mais curtas, que conferem ao pneu melhor resistência à calor e fadiga sem sacrificar a elasticidade, prolongando sua vida útil.
Em resumo, o impacto da vulcanização na indústria da borracha vai além da simples existência de produtos elastoméricos – ele se reflete também nas inovações de processo e controle de qualidade. A contínua otimização da vulcanização tem sido vital para atender às demandas cada vez maiores por desempenho (pense em pneus de alta performance ou selos para condições extremas) e por produtividade (ciclos mais rápidos, menor consumo de energia).
Aspectos Ambientais e Sustentáveis
Como muitos processos industriais históricos, a vulcanização tradicional traz desafios ambientais significativos. Por muito tempo, pouco se considerou o destino final dos produtos de borracha vulcanizada. Hoje sabemos que esses materiais, embora duráveis em serviço, tornam-se um problema ao serem descartados: borrachas vulcanizadas não possuem facilidade de reciclagem, pois são materiais termofixos, ou seja, uma vez curados não podem simplesmente ser fundidos ou remodelados.
A estrutura reticulada que confere tanta resistência também impede a reprocessabilidade. O resultado é o acúmulo maciço de resíduos – pneus usados, em especial, se amontoam em aterros e depósitos ao redor do mundo, levando décadas ou séculos para se degradar. Esse acúmulo traz riscos de proliferação de vetores de doenças (pneus retêm água, atraindo mosquitos) e, pior, riscos de incêndios tóxicos. Quando queimadas, borrachas liberam fumaça densa e poluentes perigosos, como óxidos de enxofre, metais pesados de aditivos e hidrocarbonetos aromáticos.
Além da dificuldade de descarte, o processo de vulcanização em si tem impactos ambientais diretos. A cura por enxofre gera gases e odores (quem já sentiu o cheiro de enxofre queimado em borracharias tem evidência disso). Alguns aceleradores tradicionais podem formar nitrosaminas, compostos cancerígenos, o que levou à regulamentação e substituição por sistemas nitrosamine-free em muitas aplicações, especialmente as que têm contato alimentício ou medicinal. O uso de certos metais (como óxido de chumbo em algumas formulações antigas) também apresentou problemas de toxicidade. No aspecto energético, a vulcanização requer fornos ou prensas aquecidas a altas temperaturas, consumindo bastante energia elétrica ou térmica, o que se traduz em emissões de CO₂ dependendo da matriz energética. E não podemos esquecer do impacto agrícola: a extração de látex natural em grandes monoculturas de seringueiras pode envolver desmatamento, uso intensivo de água e eventualmente agrotóxicos, levantando questões sobre sustentabilidade na cadeia de suprimentos.
Diante desses desafios, a indústria da borracha tem buscado processos alternativos mais sustentáveis e soluções para mitigar os impactos. Uma frente ativa de pesquisa e desenvolvimento é a reciclagem e reutilização de borracha vulcanizada. Reciclar borracha não é trivial, mas várias abordagens vêm sendo empregadas:
- Reciclagem Mecânica (triturar e reaproveitar): Pneus e outros artigos podem ser triturados em grânulos ou pó (conhecidos como pó de borracha ou “crumb rubber”). Esse material, embora não tenha as mesmas propriedades elásticas da borracha original, pode ser incorporado em asfaltos (asfalto borracha para pavimentação, melhorando a flexibilidade do pavimento), usado na confecção de pisos de segurança, tapetes de playground, solados de calçados, entre outros produtos. Essa é uma forma de downcycling, ou seja, a borracha é reaproveitada em aplicações de menor exigência. Ainda assim, isso prolonga o ciclo de vida do material e reduz resíduos.
- Desvulcanização Química ou Termomecânica: Uma solução mais avançada é quebrar as ligações cruzadas da borracha vulcanizada, retornando-a a um estado processável parecido com borracha crua. Esse processo é chamado de desvulcanização. Novas tecnologias têm conseguido êxito notável nessa área – por exemplo, uma empresa portuguesa desenvolveu um processo termomecânico (sem solventes químicos) capaz de reverter a vulcanização, quebrando seletivamente as ligações enxofre-enxofre e carbono-enxofre, mas preservando a estrutura polimérica principal. O material resultante é uma borracha desvulcanizada que pode ser misturada novamente a compostos e revulcanizada, praticamente fechando o ciclo. Segundo os desenvolvedores, essa borracha reciclada mantém quase integralmente as características técnicas da original, podendo substituir até 90% de polímero virgem em uma formulação nova. Trata-se de um enorme passo em direção à economia circular no setor de borrachas, pois converte resíduos em matéria-prima valiosa, com eficiência superior a 99% e sem gerar resíduos perigosos. Embora ainda emergente, a desvulcanização representa a esperança de tornar pneus e outros artefatos em recursos recicláveis de alto valor, reduzindo a necessidade de novas plantações ou petróleo para produzir borracha.
- Processos de Cura mais Limpos: Outra abordagem sustentável é aprimorar o próprio processo de vulcanização para torná-lo menos agressivo. Isso inclui a substituição de certos aditivos tóxicos por alternativas ecológicas (por exemplo, usar aceleradores isentos de aminas secundárias para evitar nitrosaminas, ou ativadores livres de metais pesados). Pesquisas exploram agentes vulcanizantes derivados de fontes renováveis e biocompatíveis. Há estudos sobre uso de enxofre obtido como subproduto industrial (por exemplo, do refino de petróleo) para vulcanização – aproveitando um resíduo de outra indústria como insumo, o que é positivo no contexto de sustentabilidade. Além disso, métodos de vulcanização por radiação (como feixe de elétrons) eliminam a necessidade de muitos aditivos químicos e podem ser realizados a temperatura ambiente, reduzindo consumo energético e evitando emissões químicas – essa técnica já é empregada comercialmente na esterilização e vulcanização simultânea de luvas de látex e na cura de revestimentos de fios elétricos, por exemplo.
- Elastômeros Alternativos (TPEs): Não exatamente uma reciclagem, mas uma substituição: em muitas aplicações, as tradicionais borrachas termofixas vêm sendo trocadas por elastômeros termoplásticos (TPE), que não requerem vulcanização. Os TPE combinam características de borracha (elasticidade) com a processabilidade de plásticos termoplásticos. Isso significa que podem ser moldados e reprocessados quantas vezes necessário, facilitando a reciclagem. Desde a década de 1970, o uso de TPEs não para de crescer e eles já ocupam espaços antes dominados pela borracha vulcanizada. Materiais como TPV (vulcanizados termoplásticos, que contêm fases de borracha vulcanizada microscopicamente dispersas em matriz termoplástica) oferecem desempenho próximo ao da borracha convencional em aplicações automotivas, calçadistas e de bens de consumo, porém com a vantagem de um ciclo de produção mais curto e sustentável. Diferente da vulcanização que exige etapas de cura e gera refugos difíceis de reutilizar, peças de TPE podem ser injetadas e, caso haja rebarbas ou produtos fora de especificação, o material pode ser regranulado e remoldado, praticamente eliminando desperdícioscompostos.com.brcompostos.com.br. Essa flexibilidade produtiva e o potencial de reciclagem fazem dos TPEs uma alternativa verde em muitas situações. É importante frisar, contudo, que para aplicações de altíssima exigência (como pneus de veículos pesados ou vedações em altas temperaturas), os termofixos vulcanizados ainda superam os TPEs em desempenho. Portanto, a tendência não é abolir a vulcanização, mas utilizá-la de forma mais inteligente e combinada a soluções complementares.
Em resumo, os aspectos ambientais da vulcanização levaram a indústria a inovar em duas frentes: tornar o processo e os materiais mais limpos, e criar caminhos para reinserir a borracha vulcanizada no ciclo produtivo. Embora desafios persistam – por exemplo, logisticamente é complexo coletar e separar milhões de pneus usados anuais – o cenário atual já conta com tecnologias e práticas mais sustentáveis do que no passado. A sustentabilidade passou de um ponto cego a uma prioridade no setor da borracha.
Tendências e Inovações na Era da Sustentabilidade
O futuro da vulcanização está sendo moldado por exigências de sustentabilidade, performance e economia. Diversas tendências e inovações despontam no horizonte, indicando como esse processo centenário continuará relevante nas próximas décadas:
- Novos Materiais e Compostos de Borracha: A busca por borrachas com propriedades específicas impulsiona o desenvolvimento de novos polímeros e composições. Por exemplo, elastômeros de base biológica (derivados de fontes renováveis, como isopreno de cana-de-açúcar) estão ganhando atenção para reduzir a dependência de petróleo. Esses materiais deverão ser compatíveis com os sistemas de vulcanização atuais ou inspirar novos agentes de cura ecológicos. Também há esforços em incorporar nanomateriais (nanotubos de carbono, grafeno, argilas nanométricas) nas formulações para melhorar a resistência mecânica e térmica sem aumentar muito o peso – isso pode exigir ajustes no processo de vulcanização, já que essas partículas interagem com o enxofre e os aceleradores de maneiras complexas.
- Inovações em Agentes de Vulcanização: Mesmo no campo da química da cura, as inovações não pararam. Estão em desenvolvimento agentes vulcanizantes híbridos que combinam diferentes mecanismos de reticulação, buscando aproveitar o melhor de cada sistema. Por exemplo, sistemas que utilizam pequenas quantidades de enxofre e peróxido simultaneamente, para obter um balanço entre resistência ao calor e flexibilidade. Outra área ativa é a formulação de aceleradores e co-agentes menos tóxicos e derivados de fontes verdes. A regulamentação ambiental tem pressionado pela eliminação de certos aceleradores tradicionais; em resposta, surgiram aceleradores à base de moléculas mais amigáveis, bem como ativadores alternativos (como óxidos de zinco de origem vegetal ou bio-baseados, e ácidos graxos de fontes renováveis) para substituir componentes de preocupação ambiental. Esses novos ingredientes prometem vulcanizar borracha com a mesma eficiência, porém gerando menos subprodutos nocivos e facilitando a disposição ao fim da vida útil.
- Aplicações Avançadas na Indústria Automotiva: No setor automotivo, a vulcanização continuará desempenhando papel crucial, porém adaptado a novas demandas. Com a ascensão dos veículos elétricos, por exemplo, há necessidade de pneus com resistência a maior torque instantâneo e peso das baterias, mas também com ultrabaixa resistência ao rolamento para maximizar a autonomia – isso requer compostos de borracha inovadores e sistemas de cura que garantam dureza na banda de rodagem sem perder elasticidade na lateral do pneu. Além disso, veículos elétricos sendo mais silenciosos, realçam ruídos de rodagem: fabricantes estão estudando borrachas vulcanizadas com melhores propriedades de damping (amortecimento de vibração) para reduzir o ruído interno e externo. Fora dos pneus, componentes como cabotagem eletrônica e sistemas de vedação para bateriasdemandam elastômeros vulcanizados que resistam a calor contínuo, exposição a produtos químicos e até fogo – impulsionando o uso de borrachas especiais (FKM, silicone, EPDM especiais) e processos de vulcanização aprimorados (como curas com doses precisas de peróxido ou sistemas de platina no caso de silicones). Também na indústria aeroespacial e petrolífera, onde condições extremas são comuns, vê-se uma tendência de desenvolver compostos vulcanizados capazes de suportar temperaturas muito altas ou criogênicas, radiação e contato com fluidos agressivos, sem degradação. Isso está levando a formulações sob medida, combinando diversos polímeros (blendas) e sistemas de cura multifásicos para atingir propriedades sob encomenda.
- Integração da Sustentabilidade no Design de Produtos: Uma inovação conceitual importante é projetar produtos de borracha já pensando em seu ciclo completo. Chamado de Design for Recycling, isso significa escolher desde o início tipos de borracha e sistemas de vulcanização que facilitem a futura reciclagem ou reutilização. Por exemplo, optar por um determinado sistema de vulcanização reversível, em pesquisa atualmente, que use ligações cruzadas que podem ser “desfeitas” sob determinado estímulo (calor controlado, química ou mesmo luz UV) para permitir a reciclagem total do produto. Embora ainda incipientes, essas chamadas ligações covalentes dinâmicas ou vínculos dissociáveis são um campo de investigação promissor, pois podem dar origem a borrachas auto-reparáveis (que se reconstituem após um corte, mediante calor) ou reprocessáveis. Imagine pneus cujo material pudesse ser re-fundido e re-moldado em novos pneus ao fim da vida – esse tipo de ruptura tecnológica pode surgir da convergência entre química, engenharia e pressões ambientais.
- Termoplásticos Vulcanizados (TPVs) e Híbridos: Conforme mencionado, os elastômeros termoplásticos têm ganhado terreno. Uma tendência específica são os TPVs, nos quais a borracha é vulcanizada dinamicamente durante a mistura com um plástico termoplástico (como polipropileno). O resultado é um material com ilhas de borracha vulcanizada dispersas numa fase termoplástica contínua – combinando a resiliência da borracha com a reciclabilidade do termoplástico. Os TPVs já são usados em perfis de vedação automotivos, substituindo o EPDM vulcanizado tradicional, e em componentes como manoplas e revestimentos. Espera-se que novos TPVs com borrachas diferentes (talvez incorporando borracha natural vulcanizada dinamicamente, ou borrachas especiais) cheguem ao mercado, ampliando as aplicações onde se pode evitar um termofixo puro sem perder desempenho. Esses materiais híbridos representam uma ponte entre a vulcanização clássica e a processabilidade moderna, e exemplificam bem o futuro: combinações inteligentes de materiais para atingir sustentabilidade e funcionalidade.
Em conclusão, a vulcanização na era da sustentabilidade não é um conceito estático preso ao passado, mas sim uma área em contínua evolução. Desde a descoberta fortuita de Goodyear até os avanços atuais em química verde e reciclagem, o que vemos é uma trajetória de inovação constante. A vulcanização permitiu a expansão da indústria da borracha no último século e meio, e agora ela própria está se reinventando para permanecer relevante num mundo que exige processos mais limpos e circulares. Novos materiais, técnicas aprimoradas e uma mentalidade de ciclo de vida completo apontam para um futuro em que poderemos continuar contando com borrachas de alto desempenho – em pneus, selos, dispositivos médicos e além – sem comprometer o meio ambiente. A capacidade de adaptação será a chave: assim como a descoberta de 1839 transformou a borracha para sempre, as descobertas do século XXI certamente redefinirão como vulcanizamos e reutilizamos esse material tão versátil.
Em suma, vulcanização é sinônimo de transformação da borracha. Entender sua história e dominar suas técnicas clássicas e modernas é fundamental para qualquer profissional do setor. E ao olharmos adiante, fica claro que os próximos capítulos dessa história serão escritos com tinta verde da sustentabilidade, guiados pela ciência e pela inovação contínua. Afinal, assim como o nome de Goodyear ficou eternizado na indústria, as soluções que equilibrarem desempenho e respeito ambiental serão o novo legado duradouro da vulcanização no século XXI.
Comentários ()